A robotics expert is helping her inventions navigate through difficult, tight spaces using unique soft materials that contract and expand on demand.
In the last few years, oil and gas companies have begun to rely on robots to travel miles of undulating pipelines checking for weaknesses, cracks, and blockages.
But it’s been much harder to make mechanical robots small enough to squeeze through the centimetre-wide tubes commonly found in everything from aircraft engines to oil refinery machinery.
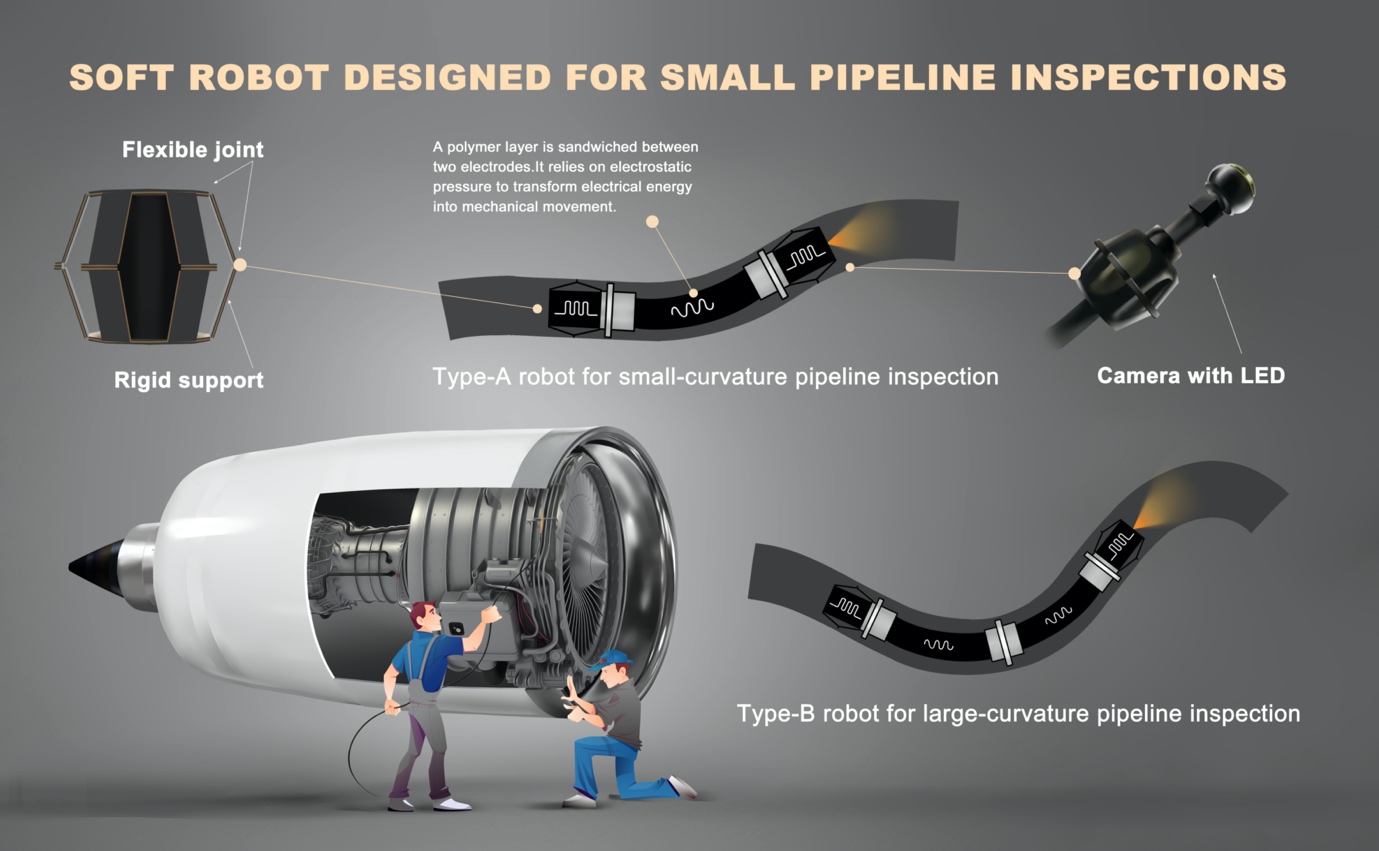
Huichan Zhao and her collaborators are creating soft robots that use similar movement techniques to earthworms for potential use in inspecting small pipelines, such as those found in aircraft engines.
Huichan Zhao, a mechanical engineer at Tsinghua University in China, thinks soft robots, without wheels or other chunky components that can’t fit through a gap or squeeze around a tight corner, could be the solution.
Soft robots often attempt to copy the motion of nature’s soft structures, such as elephant trunks and the tentacles of an octopus, explains Zhao. Soft structures can often move in more complex ways than conventional robots with joints, she says.
Earlier this year, Zhao and her collaborators published the details of a soft robot designed to mimic the movement of earthworms, which could be used to perhaps inspect the narrow pipes found in machinery such as aircraft engines. One day, she hopes her earthworm-inspired robot could replace the fibre-optic cables typically used to inspect these pipes today.
“Using fibre optics to see inside pipes requires a skilled engineer to manually control the process,” she explains. “Using a robot that navigates the pipe itself saves time and effort.”
Worming through
An earthworm travels forward using a physical process called peristalsis, which relies on the rhythmic contraction and relaxation of muscles in a series of connected segments. Ring-like muscles around the worm’s diameter can change its body thickness to either swell and grip the inside of a tunnel or shrink to pass through. Longitudinal muscles along the length of the creature’s body push the worm forwards or backwards.
So, if an earthworm fixes its rear ring muscles against a tunnel’s insides and then stretches its longitudinal muscles to push forwards, followed by fixing its front ring muscles and then contracting its longitudinal muscles again, its body nudges forward.
Most importantly for soft robot design, because an earthworm moves purely through muscle expansion and contraction, it doesn’t need any complicated moving parts and mechanisms. This makes it relatively easy for scientists to copy.
To mimic this movement pattern, Zhao focused developing smart materials called dielectric elastomer actuators that can squeeze and relax in response to an electric supply being turned on and off.
These smart materials sandwich a polymer layer between two electrodes and rely on electrostatic pressure to transform electrical energy into mechanical movement.
Using dielectric elastomer actuators that work in different directions when stimulated by electricity to mimic the earthworm muscles, Zhao could build a robot that uses the same strategy as an earthworm to move through a narrow pipe: anchoring one end against by expanding to brace against the pipeline walls, and then extending along it.
By attaching a small camera to the front of the robot, users can check the insides of the pipe as the robot nudged along.
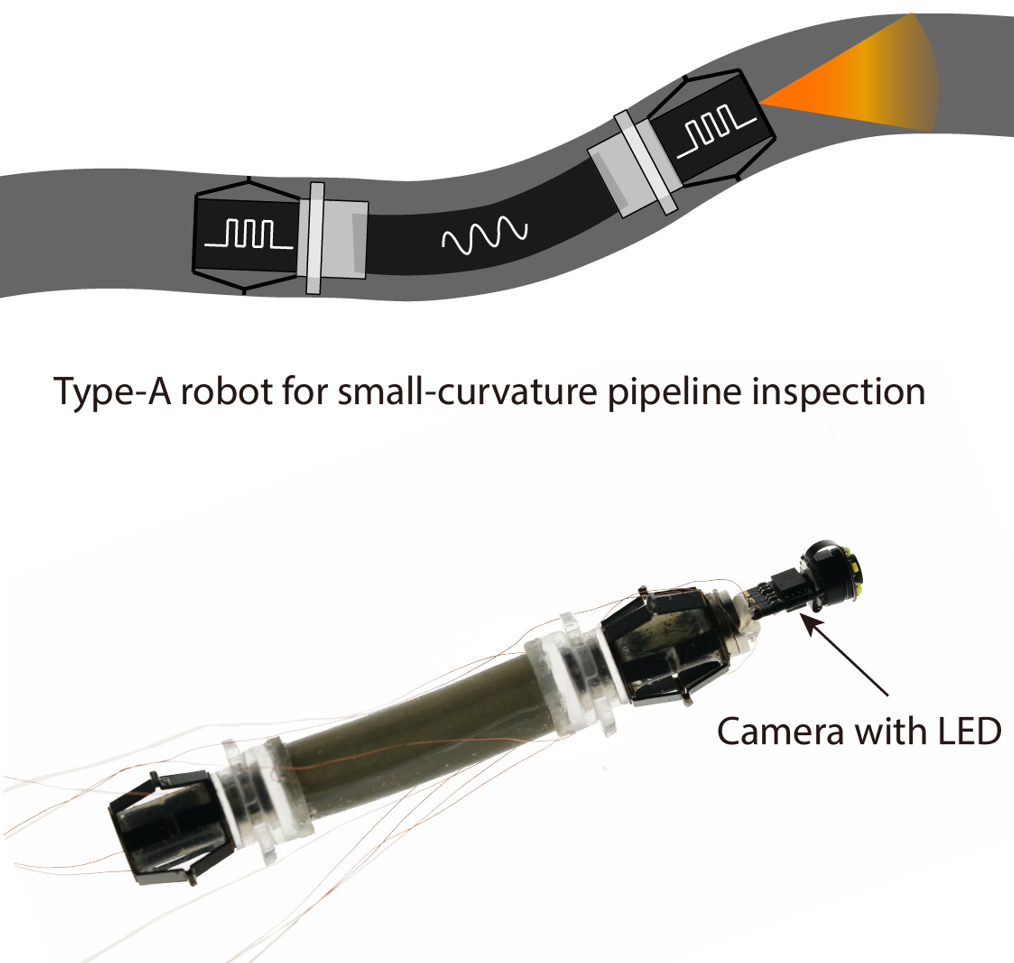
This soft robot that uses the same movements as an earthworm to move through a narrow pipe – anchoring by expanding its front or back sections to brace against the tunnel or pipe walls, and then extending its middle sections to move forward.
Published in the journal Science Robotics1, the soft robot is a demonstration of how the concept could work, but many details must be ironed out before it could be used in practice.
For instance, because the electricity is supplied to the robot through trailing wires, this increases drag and might prevent the robot from making headway through some pipelines. A better design would rely on portable high-powered batteries, says Zhao.
“As far as I know, there are no such robots in use. Many challenges need to be overcome, such as how to effectly connect an energy supply, and improve controllability and reduce cost,” she says. “I think, it still needs five to ten years of fundamental research.”
Rapid rise for robotics researcher
Zhao is still in her 30s, having graduated with a double degree in mechanical engineering and economics from Tsinghua in 2012. She then carried out postgraduate studies and training in the United States, including time working on using integrated sensors to improve robot touch sense at Cornell University in the United States, and later at the Microbiotics Laboratory at Harvard University, also in the US. When she returned to Tsinghua in 2018, she was one of the youngest faculty members at the time.
Her research with robots is not confined to pipelines. With collaborators, she has previously developed a tiny flapping robot and eventually got it to fly. And in early 2020, she and other team members developed an early throat swab sampling robots in response to the outbreak of the COVID-19 pandemic. The swabbing robot looks more like a conventional robot: a seven-jointed robotic arm and a small robotic hand that can grab cotton swab. It was designed to relieve the burden on human samplers, reducing the risks of infection and contamination via the sampling process, explains Zhao.
Healthcare should be a useful arena for soft robots, she adds. “They could be used as surgical robots,” she notes. “I think they could become quite desirable, as they would do less harm to tissues than hard instruments.”
So, while robots that look like humans often receive the most of the attention, it could be the small soft robots inching around our pipelines or in the body that really have an impact on day to day life.
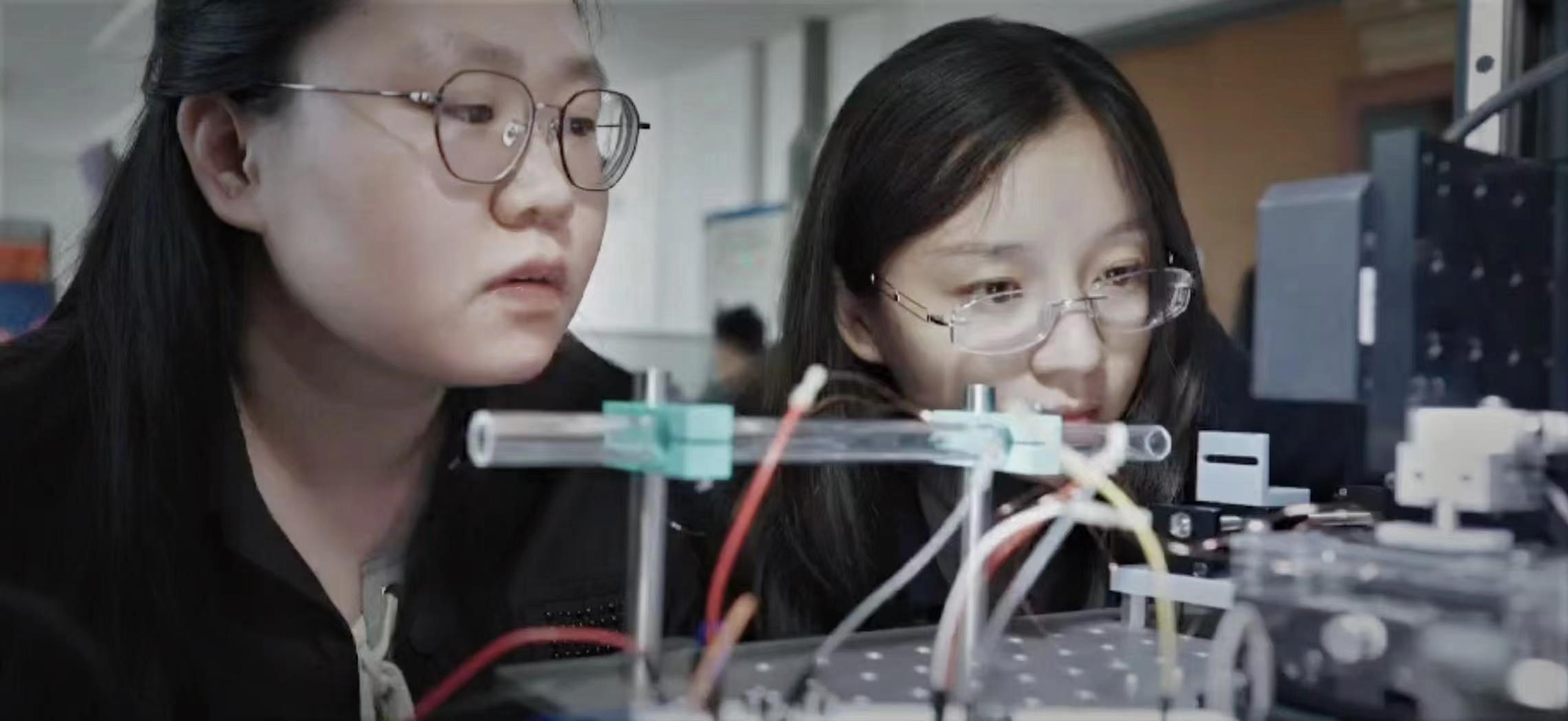
Huichan Zhao (right) tests one of her robotic creations
Reference
Tang, C., Du, B., Jiang, S., Shao, Q., Dong, X., et al. A pipeline inspection robot for navigating tubular environments in the sub-centimeter scale Science Robotics 7(66) (2022) doi: 10.1126/scirobotics.abm8597
Editor: Guo Lili